Junair Spraybooth Installation for AW Repair
Since its inception in 1998 AW Repair Group have rapidly grown to become one of the leading accident repairers in the UK, with a strong belief in investing in purpose-built high tech repair facilities, equipment and technologies to ensure they remain at the forefront of the accident repair market.
Following new Junair Booth installations at their Markham Vale and Newark sites, AW Repair were so impressed with the energy saving benefits and increased productivity that they rolled out upgrades across the group. The most recent being a new drive through Junair Spraybooth at their Denaby site.
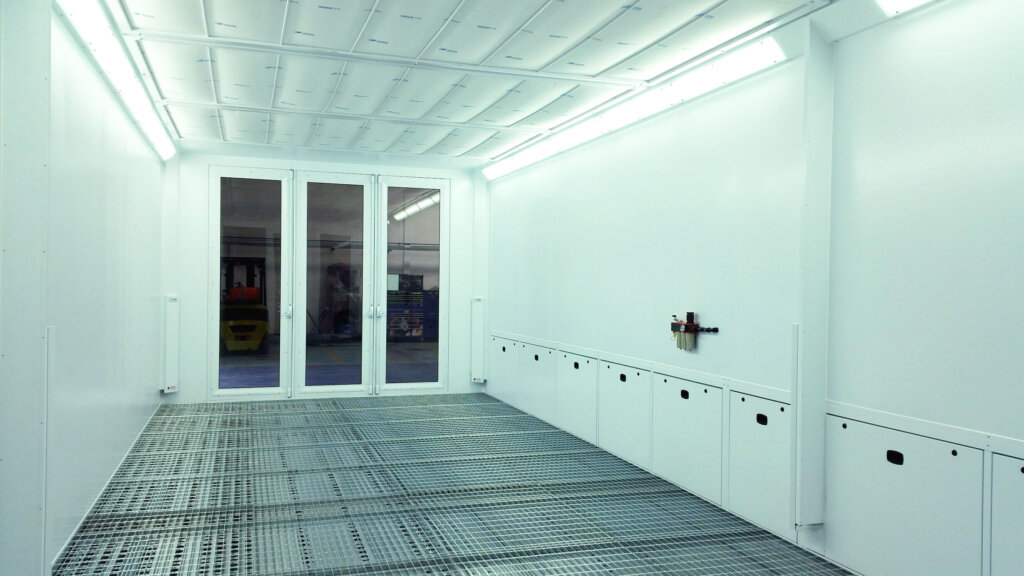
Junair Drive Through Spraybooth Installed at Denaby
A 10.5m long and 3.6m high Junair 3 series drive through spraybooth was installed at AW’s Denaby site featuring a LEVAC fully gridded floor to harness the benefits of a full downdraught floor whilst eliminating the need to excavate the existing floor. A very low 140mm high raised base accessed by a 1m long ramp allows an easy entrance to the spray booth through a glazed 3 leaf door set. The extended length and height ensure AW can now comfortably paint any van including Lutons.
The drive through loading system allows cars to be loaded and unloaded easily in either direction through either end of the spraybooth. This maximises workshop space and provides the bodyshop with a more efficient workflow in comparison to more conventional drive-in, back-out loading systems.
The speed of the repair process is key to AW Repair Group as they offer their customers 24 hour and same day repairs. Thanks to the Junair patented QADS systems their process time will be considerably improved. Junair QADS are an advanced system which supplies auxiliary air flow at low level from the corners of the spraybooth cabin. The clean, filtered and heated air creates the ideal environment for the fast, controlled flash off of waterborne base-coats and the rapid through curing of low VOC top coats as QADS also works on the bake cycle. QADS can reduce the overall paint drying and curing process times by around 35% meaning that one spraybooth can handle many more jobs, substantially increasing capacity and revenue. The financial savings from lower energy consumption combined with the ability to process more vehicles offers a rapid return on a QADs investment.
Energy Efficient Spraybooth Installations from Junair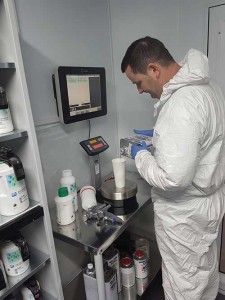
Junair’s LED lighting was installed not only ensuring optimum colour rendition for the operatives but Junair LED lights also have energy saving benefits; having installed LED lighting at other AW sites they had no hesitation in adding them to the energy saving pack. Junair LED lights also qualify for ECA tax relief making them even more attractive.
The 3 series was also fitted with Fuel Saver Mode and Variable Speed Drives maximizing the efficiency of the spraybooth. The Junair Fuel Saver Mode is fully automatic requiring no operator input, therefore the savings are guaranteed. Most of the energy used by a spraybooth goes on heating up the external air to meet the required condition inside the cabin. FS Mode automatically changes the air handling plant from full fresh air intake to recirculation during idle and flash off modes, substantially reducing the air heating costs.
Automatic Variable Speed Drives have been fitted to the 3 series. The use of variable speed drives on spraybooth fan motors is nothing new, however Junair have developed a unique system that varies the airflow volume to suit the process. The system is fully automatic, requiring no operator selection so the energy savings are guaranteed. Reducing the airflow through the cabin means lower fuel and electricity costs. 100% airflow is not required when the booth is standing idle or when vehicles are being loaded and unloaded.
The energy efficiency of the Denaby will now have running costs on a par with Markham vale – the first of the sites to undergo these energy saving upgrades.
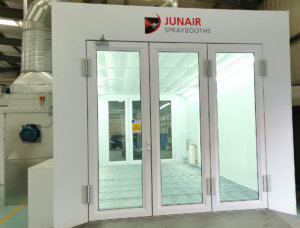
Grahame Kitchin, Sales Director, Junair Spraybooths commented “It’s a pleasure to be working with AW Repair Group again. I’m thrilled that they were so pleased with our other installations that they turned to us to upgrade their other sites. I am confident the benefits delivered at AW’s other sites will be repeated at Denaby”
Andrew Walsh, Managing Director, AW Repair Group commented “I’ve seen measurable results with the 3 Series spraybooth Junair installed at Markham Vale and Newark. Looking at the increased labour sales figures it made complete sense to roll out the installations including the energy saving packages across the whole business. The new spraybooth is processing 13 cars a day, the results speak for themselves.”
Written by